I hope you all had a great Thanksgiving! (Or a great Thursday, if you’re not in the U.S.) We had a perfectly quiet day; just the two of us, a little crafting, a lot of turkey. A good way to celebrate Branden being home.
I promised to show you the yarn I got at the mill, so let’s start there.
My stash is at full capacity right now, so I was working very hard to keep purchases to a minimum. I’ve been watching this yarn for a sweater for a year now, but I also have four sweaters lined up in the queue, and so decided to wait on sweater quantities. Instead, I found these beautiful skeins of laceweight in the sale bin.
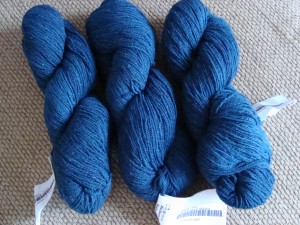
Plenty for a large project, and how could you resist that color?
I also bought some of their handpainted yarn, which has a really interesting texture when dyed. It’s 100% wool yarn, and they use the same dye for the solids, but the handpaints all look like chenille when they’re knit up (And the solids don’t). I asked, and they don’t really know why this happens with the handpaints, but I’d love to find out. It’s a completely unique look as far as I know, and I really like it.
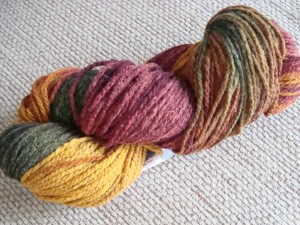
This yarn is destined to be a hat. I think I’ve complained here before about the sad fact that I am not a hat person. I can’t recall ever having a hat that I liked, and so I have spent years and years going around with a cold head in the winter. This doesn’t really bother me, but now that it’s getting nippy outside in the mornings, it would be nice to have a hat that I can at least stand to wear on the really cold and windy days.
So, I sat down on Saturday night and cast on for this:
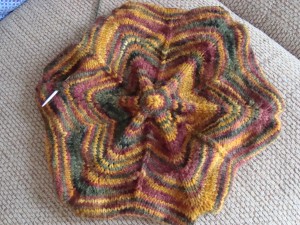
It’s a simple tam style, which I’m completely making up as I go (I’m sure you’re surprised). I love how it turns the handpaint into a flower, and I really like the strong radial lines popping up in the center. As a knitted object, I like it very much. As a hat? As in something I would actually wear on my head? That’s a little harder.
Part of the problem is the color. I love the handpainted look and I definitely want to keep it, but I think there’s just too much of it. When the flower part was small, I was completely in love. As it grew larger, it just got too busy. Also, the points. Love them as an abstract knitted object, but on my head, they make me think of the Mario Bros. mushroom cap. Not exactly the look I’m going for.
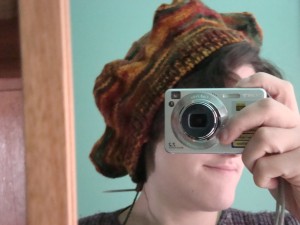
It’s also turned out too big. I blocked it on the needles last night, and I definitely overshot the proper radius of a tam. And so today I rip. Not all the way, but back far enough that I like it again, and then I’m going to start over from there. The good news is that I kind of like the way it feels on my head, so now we just need to work on how it looks.
So, progress. And ripping. They seem to go hand-in-hand, don’t they?